Casting
At Advect Process, offers casting products as we specialize in the design, development, and production of precision components, semi-assemblies, and fully finished assemblies tailored to your specific requirements. Our capabilities extend to creating custom solutions of casting components based on customer drawings or samples, utilizing advanced technologies such as reverse engineering, 2D/3D designing, blue-ray scanning, 3D printing for prototype development, and CAD & CAM software.
Our products based on casting types and applications
Types of Casting
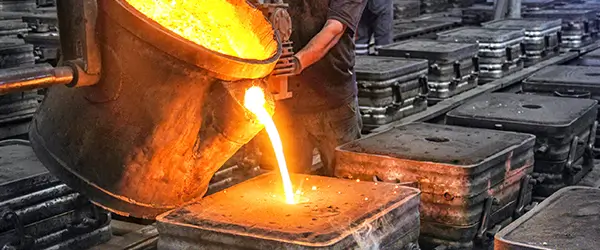
Sand Casting
Sand Casting is still the most prevalent form of casting. It is a conventional moulding and metal casting process as the mould may be poured without further conditioning. The mould is formed around a pattern by ramming sand, mixed with the proper bonding agent, onto the metal or wood pattern. Then the pattern is removed, leaving a cavity in the shape of the casting to be made. Sand cores are placed if internal cavities or undercuts are required. Molten metal is poured into mould and after it has solidified the mould is broken and castings are removed for secondary process and final finishing.
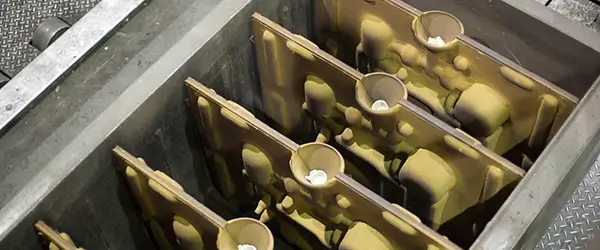
Shell Moulding Casting
Shell Moulding Casting is a process for producing simple or complex near net shape castings, maintaining tight tolerances and a high degree of dimensional stability. Shell moulding is a method for making high quality castings. These qualities of precision can be obtained in a wider range of alloys and with greater flexibility in design than die-casting and at a lower cost than investment casting.
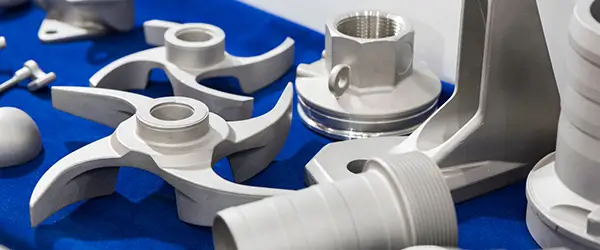
Investment Casting
Investment Casting is manufacturing process for making small, accurate castings in refractory alloys using a mould formed around a pattern of wax or similar material which is then removed by melting.lt offers Superior surface finish, Complex, near net geometries, Wide range of alloys, Fine detail
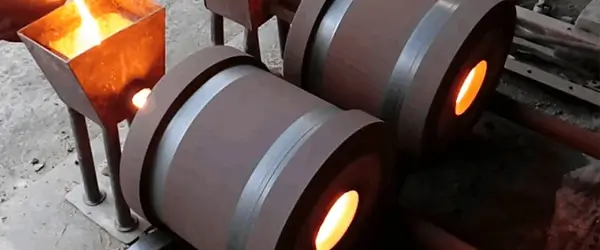
Centrifugal Casting
Centrifugal Casting or Rotocasting is a casting technique that is typically used to cast thin-walled cylinders. It is typically used to cast materials such as metals, glass, and concrete. A high quality is attainable by control of metallurgy and crystal structure.
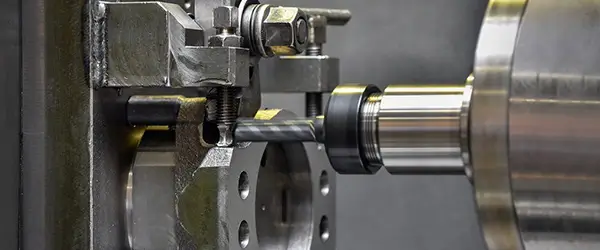
Precision Machining
Precision Machining is a process of cutting of excess from a larger piece of material to created a small piece of exact shape and size that will fit exactly where needed to smoothly carry out its desired task and as such a wide range of machinery is used.
Casting Process Flow Chart
2d / 3d Designing & Die/Mould Preparation
In-house 2D/3D design, reverse engineering, and prototype development for casting parts.
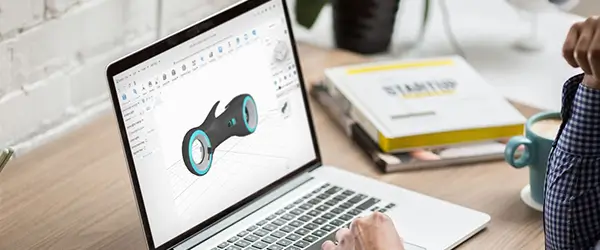
Mould Creation on VMC
We are having in-house CNC / VMC A state of Art Machining facility where we are developing Tools & Moldsfor Casting Parts.
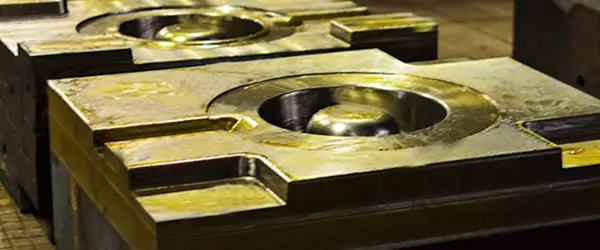
Metal Pouring Process
Metal pouring process, ensuring precision in the crafting of casting parts.
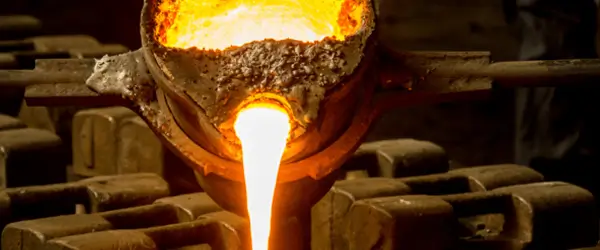
Casting Knockout Process
We remove all castings from the mold box and brake the Runner & Riser.
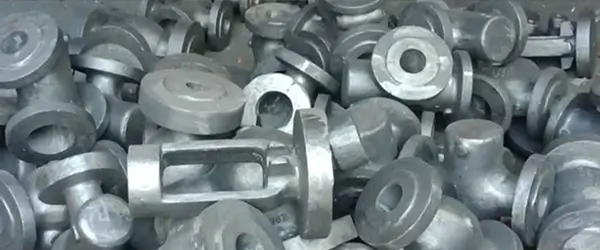
Shot Blasting, Fettling & Cleaning Process
Runner and riser removal, grinding, shot blasting, and thorough cleaning process.
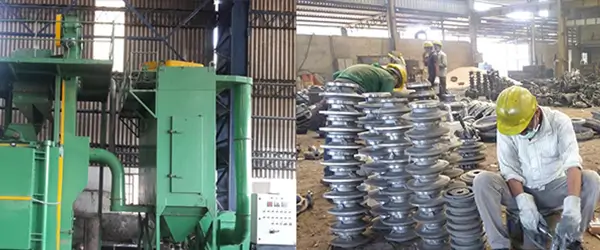
Finish Machining Process
State-of-the-art facility for CNC, VMC, VTL, and SPM drilling.
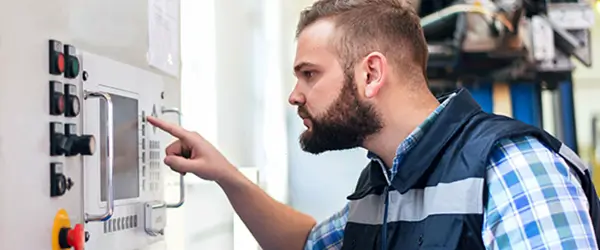
Heat Treatment & Surface Coating Process
Outsourced heat treatment and surface coating for client-specific drawing requirements.
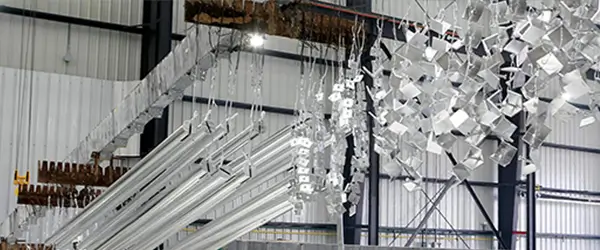
Pre-Dispatch Inspection
Rigorous quality checks ensuring adherence to client's specifications before dispatch.
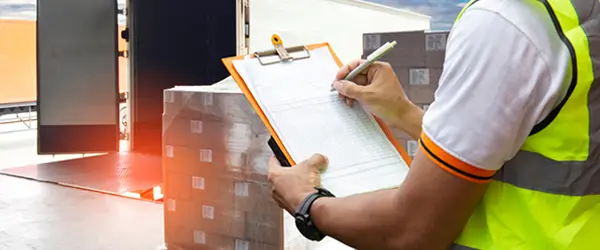
Applications
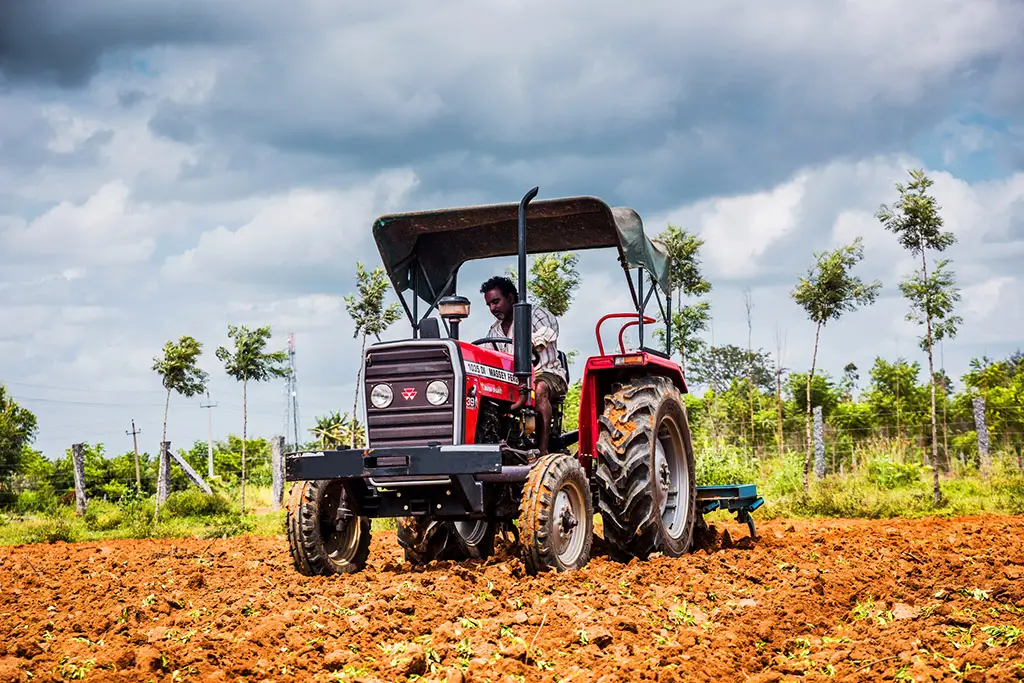
Agriculture
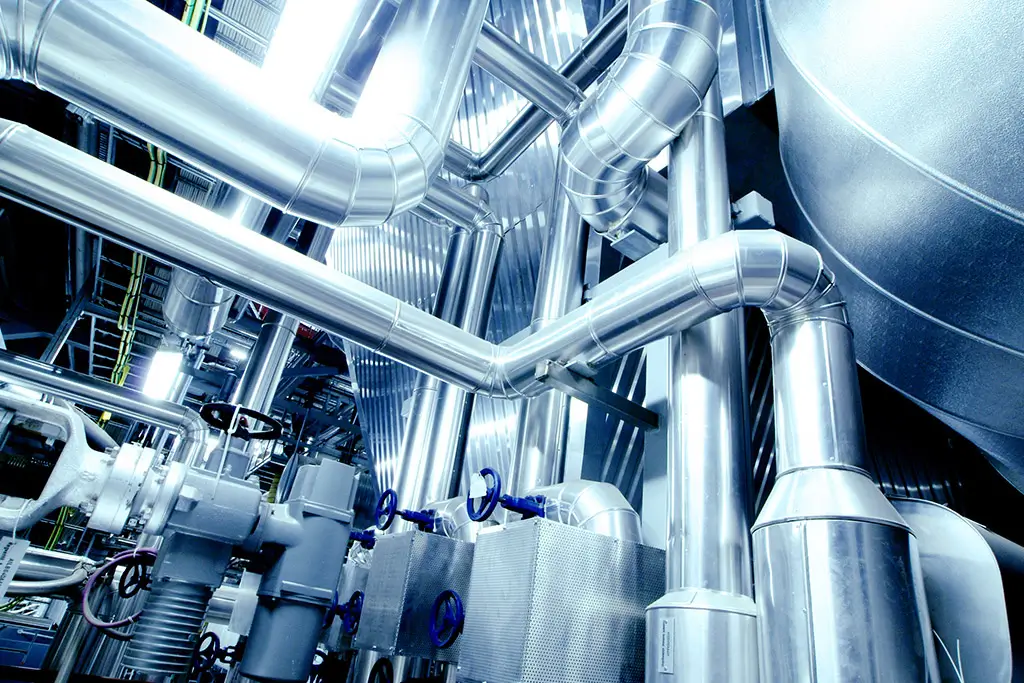
Fluid Handling
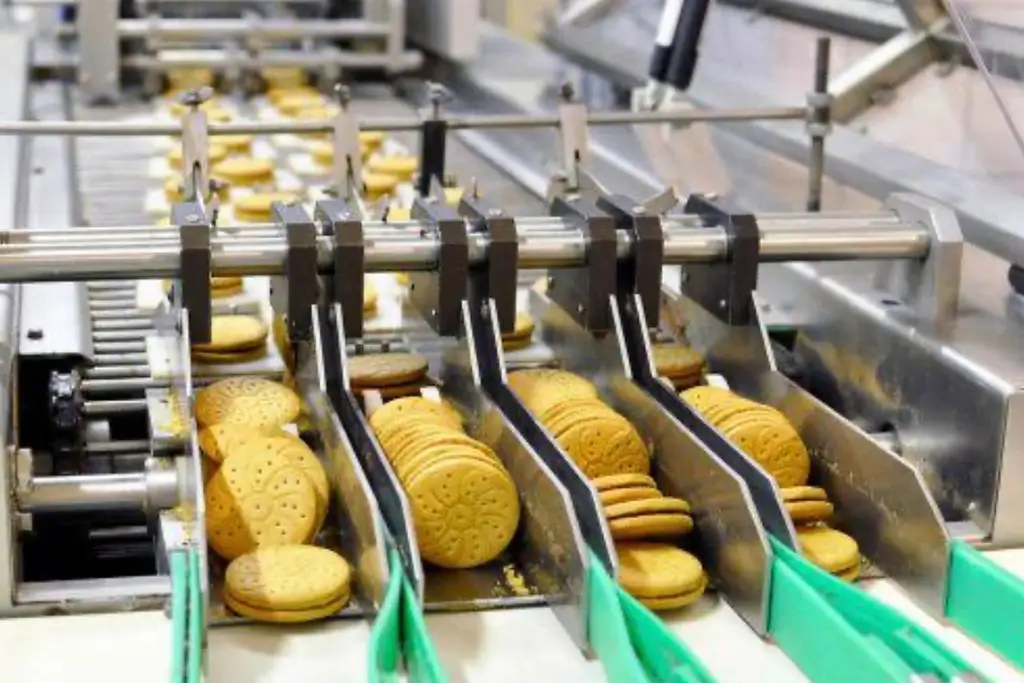
Food Processing

Government & Military
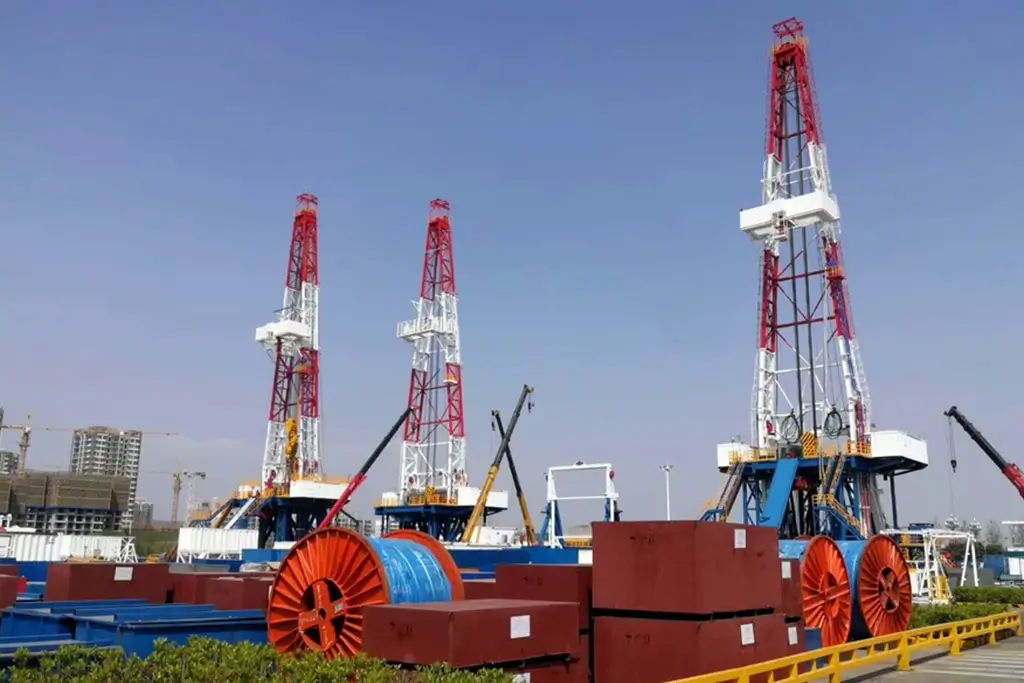
Lifting & Swivels
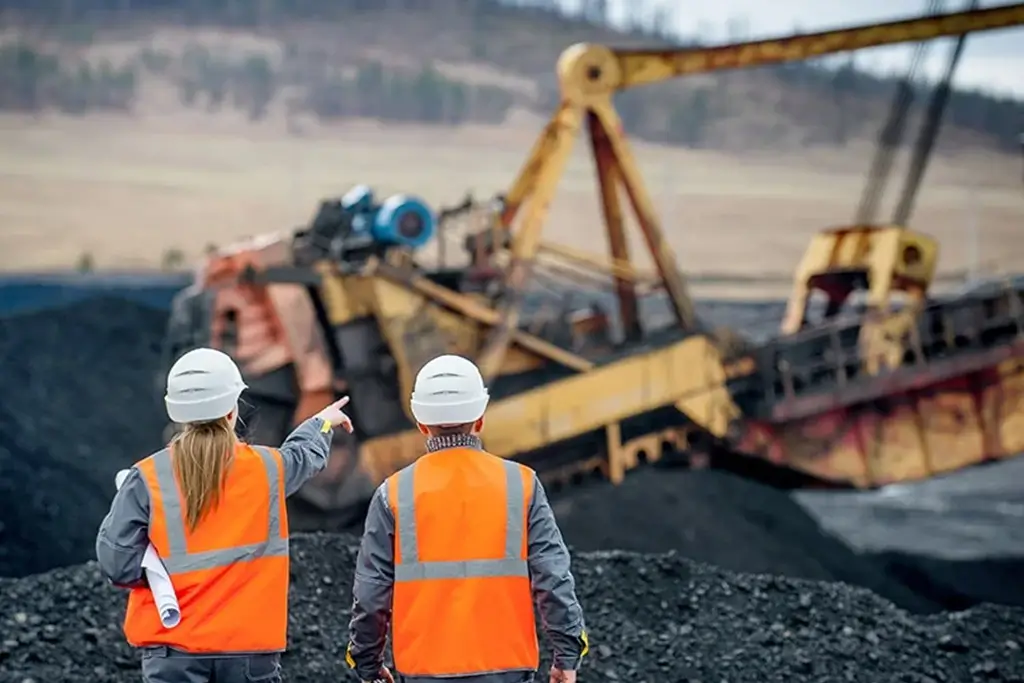
Mining
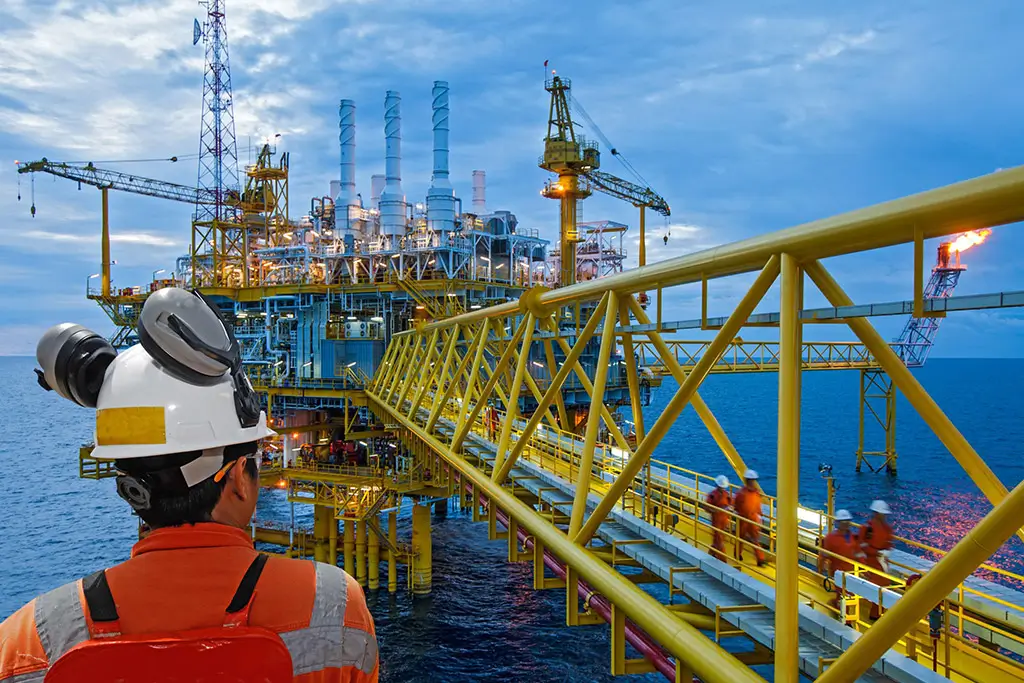
Oil & Gas
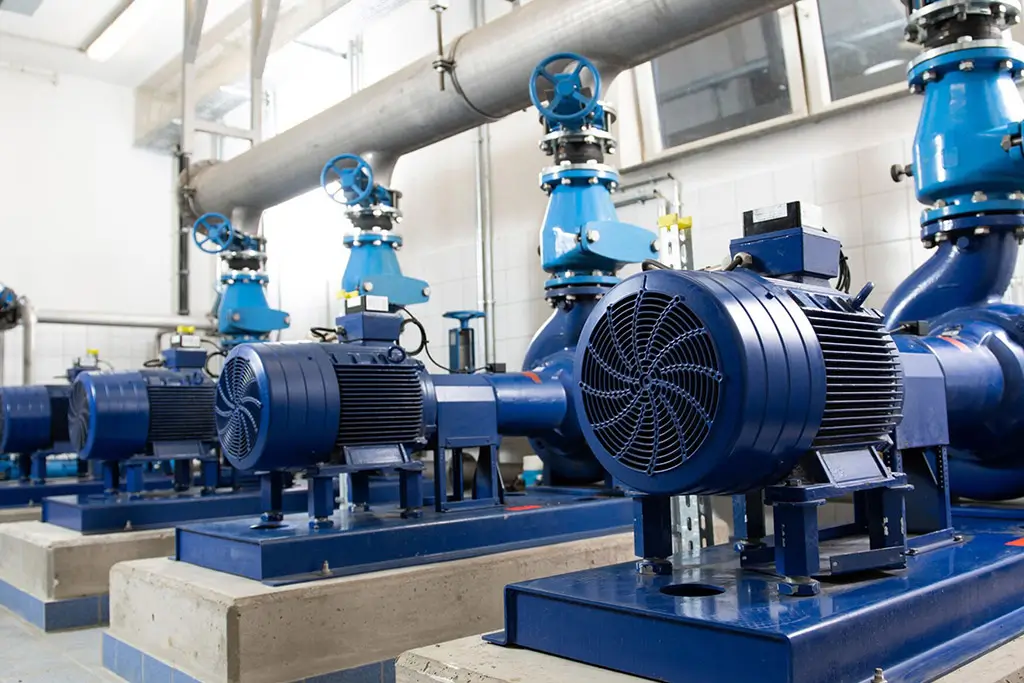
Pumps & Valves
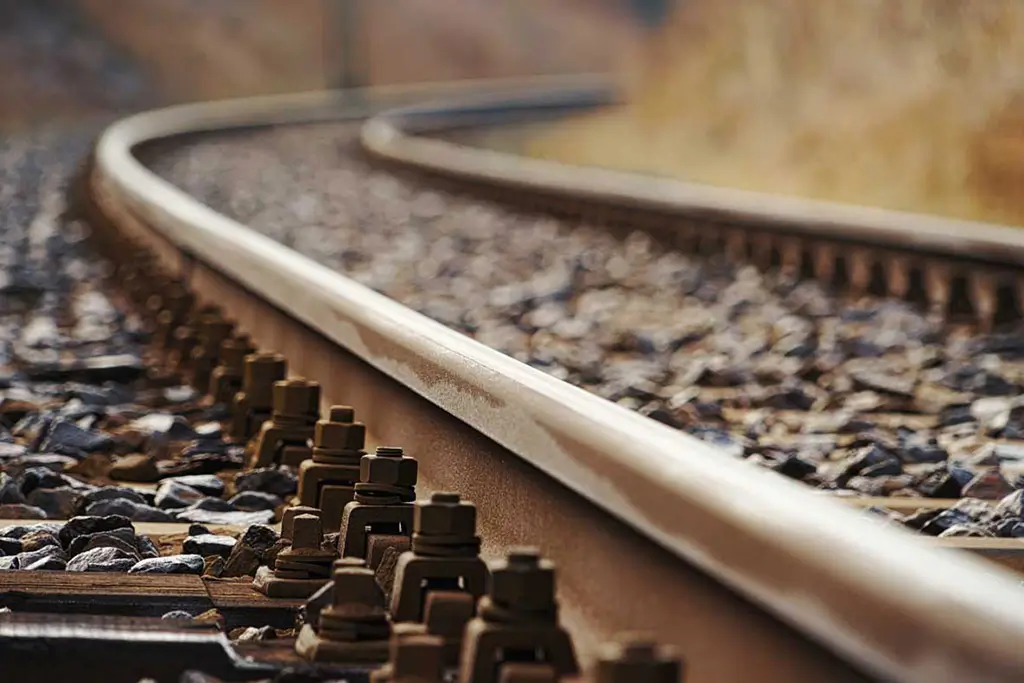
Rail Road
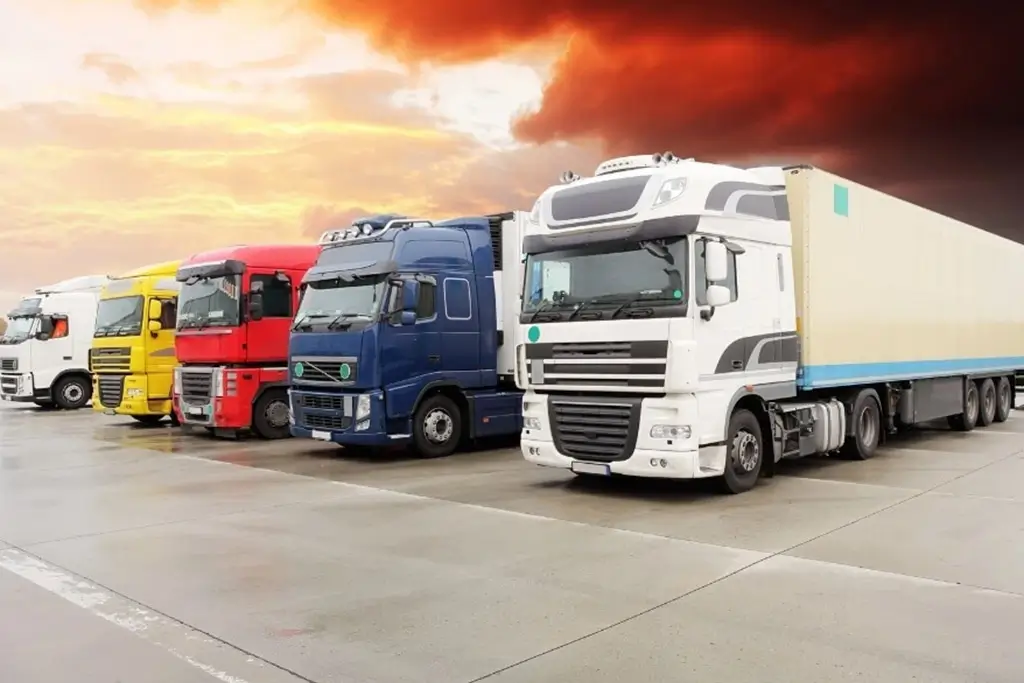
Transportation
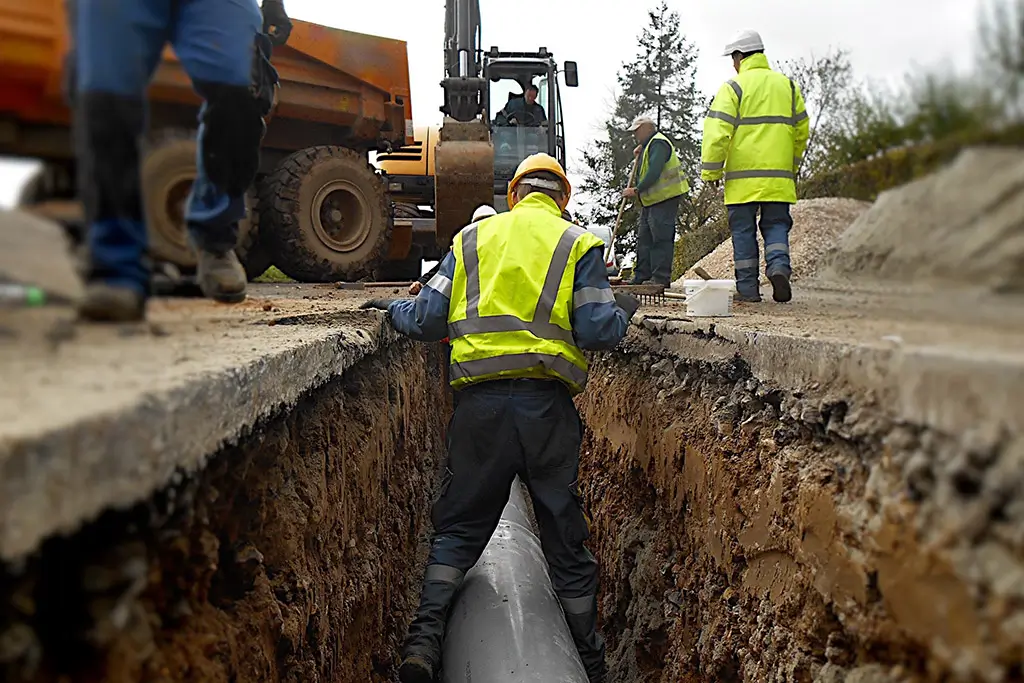
Utility
Example of Casting Parts
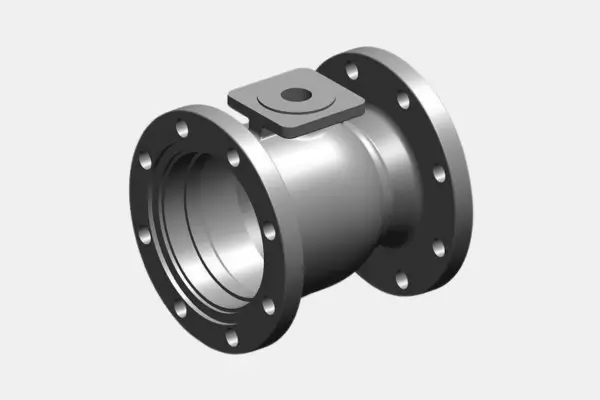
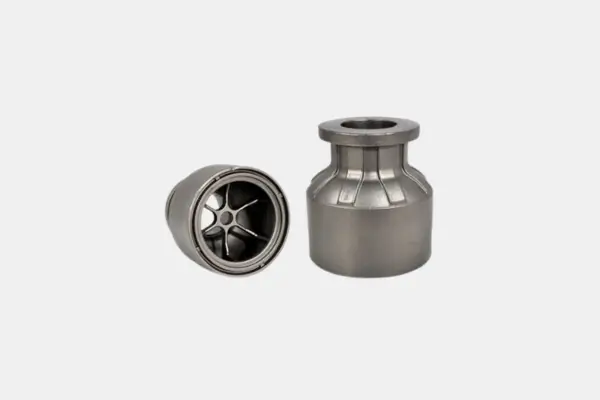
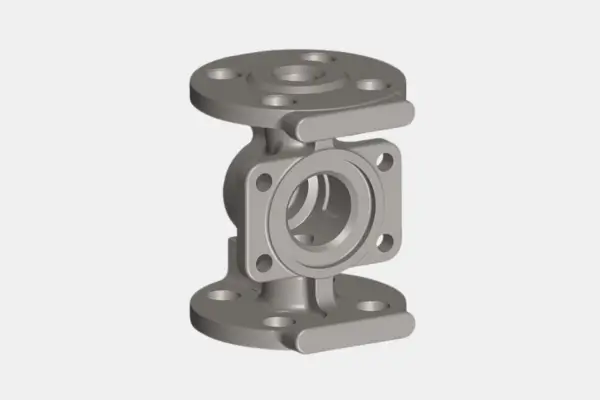
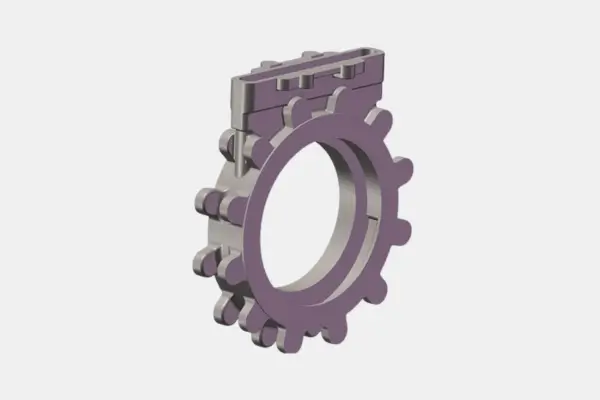
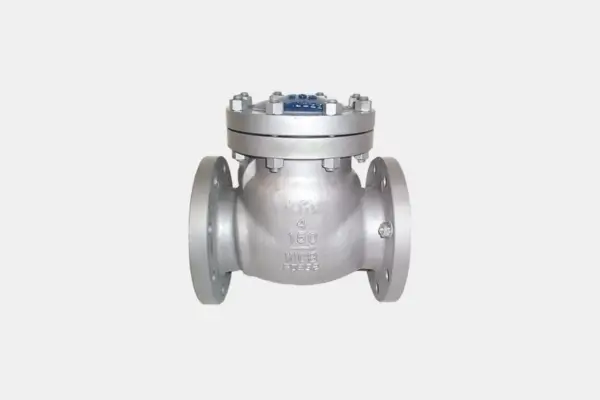
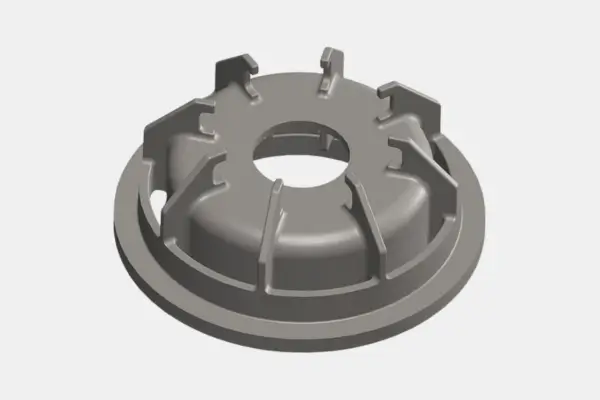
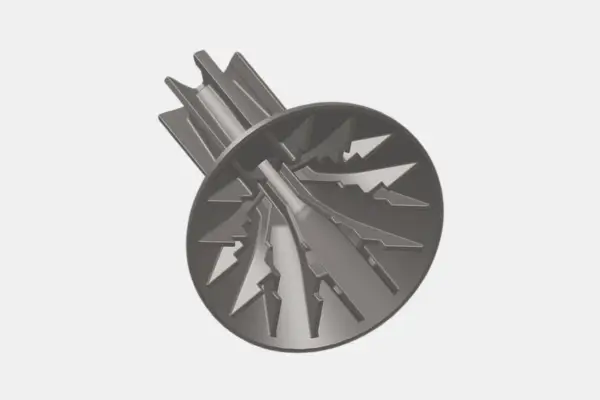
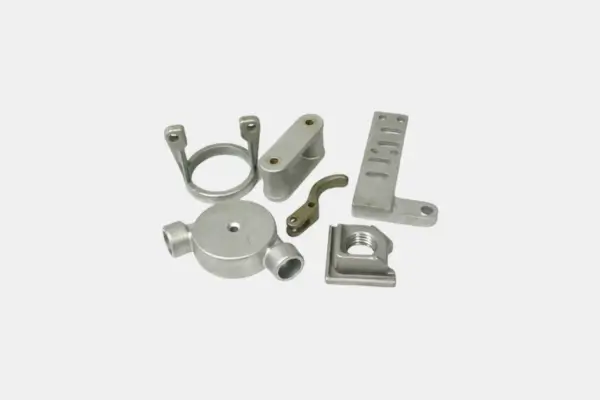
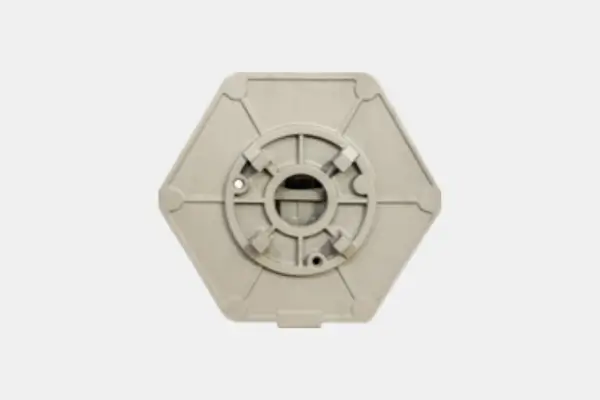
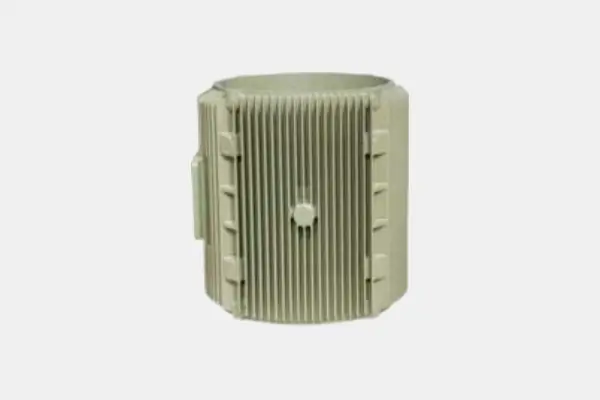
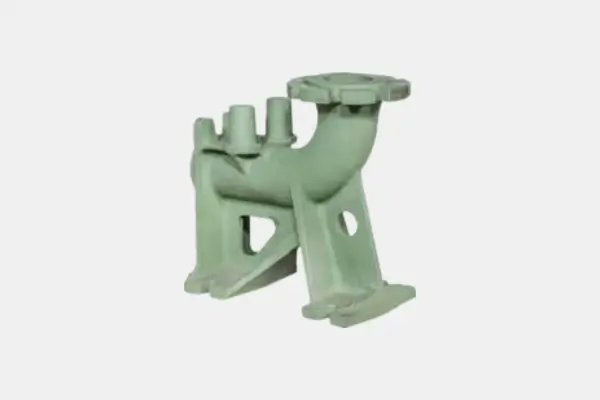
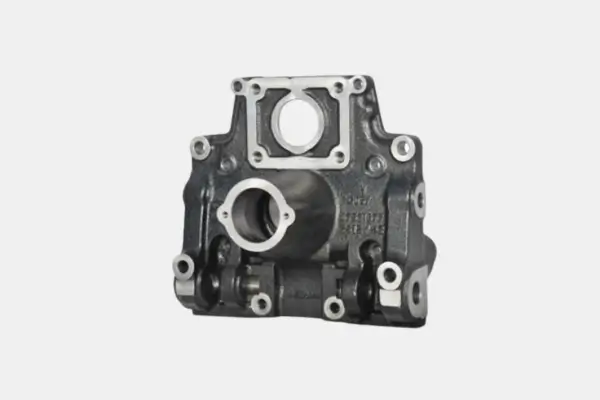